Understanding the Polymer Injectable Molding Procedure One Step at a Time
In today's world, in which efficiency and precision are vital in manufacturing, injection molding stands out as a highly effective production method. This advanced process allows for the rapid creation of intricate plastic parts with notable accuracy, making it a preferred choice for numerous sectors. From retail items to automotive components, the versatility and scalability of injection molding services have revolutionized how products are made.
Understanding the details of the plastic injection molding process is important for businesses looking to leverage this technology. Whether plastic injection molding service are a product designer, an engineering professional, or a production manager, grasping the sequence of events of how molten plastic is turned into finished products can empower you to make strategic decisions. This article will walk you through each stage of the process, providing insights into how the injection molding process can enhance your manufacturing processes.
What is Plastic Injection Molding?
Plastic injection molding is a technique used to form a wide variety of plastic products. This method involves forcing molten plastic into a pre-designed mold to form an object. The molds are commonly made from steel or aluminum and can be reused for multiple production cycles, making the process efficient for high-volume manufacturing.
In the course of the injection molding procedure, plastic pellets are toasted until they liquefy and then put into the mold under significant force. Once the plastic solidifies and solidifies, the mold is released, and the finished piece is removed. This method is well-regarded for its potential to create intricate designs with high precision and repeatability, leading in reliable quality across many units.
The versatility of plastic injection molding enables its use for a wide range of uses, from retail items to industrial components. Multiple categories of plastics can be used, enabling manufacturers to tailor properties such as durability, malleability, and tolerance to temperature or substances, according to the specifications of the end item.
Important Phases in the Injecting Molding
The molding procedure starts with the setup of the raw material, typically in the shape of plastic pellets. These particular pellets are fed into a hopper where they are melted until they reach a molten state. The temperature is precisely controlled to ensure that the material flows easily into the mold. This setup is crucial as it affects the final attributes of the molded part.
Once the material is melted, a oscillating screw or a piston injects the plastic into a tight mold at intense pressure. The mold is designed to shape the plastic into the intended configuration, which can extend from simple components to intricate geometries. The pressure applied during injection ensures that the mold cavity is thoroughly loaded, reducing defects in the finished product.
After the injecting phase, the material is given to solidify and set inside the mold. This chilling time is contingent on the thickness of the part and the kind of plastic being used. Once the part has chilled sufficiently, the mold is released, and the finished product is ejected. At this stage, any required trimming may be performed before the part is prepared for use or further construction.
Benefits of Using Injection Molding Services
A primary benefits of using injection molding services is the speed they offer in manufacturing mass amounts of parts. Once the mold is created, the process can quickly duplicate the desired shape with little waste of resources. This high efficiency can greatly reduce manufacturing expenses over time, especially for high-volume production where consistent quality and rapid output are crucial.
Injection molding services also provide a high degree of flexibility in design. With cutting-edge technologies, manufacturers can produce complex shapes that may be difficult to achieve through alternative methods. This flexibility allows businesses to think outside the box and customize their products, catering to specific market needs without sacrificing quality or extending lead times.
Another significant benefit is the durability and strength of the parts produced through injection molding. The process allows the use of different materials, including strengthened plastics, which can enhance the product's longevity and performance. By choosing injection molding services, companies can guarantee that they receive high-quality components that meet stringent industry standards, which ultimately leads to increased customer satisfaction and brand trust.
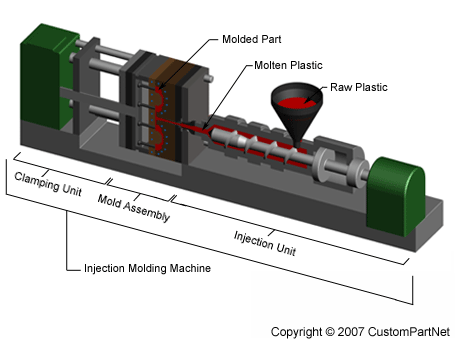